Inertisation
The inertisation is performed to secure the tanks or equipment such as reactors, mixers, centrifuges, glove boxes, enclosed areas or other. The replacement of oxygen with nitrogen or other inert gas, allows to avoid an explosion or fire where there are fluids that may generate flammable vapors. This methodology is also applied in the Food, eg. in silos containing flour, preventing the proliferation of insects contained in the same. Another example of inertisation occurs in cold rooms for storage of fruit, in the server rooms, in blenders of powders; most common case is that of the "load aluminum powder".
The inertisation is performed to secure tanks or process machines such as, for example: drying tunnels, centrifuges, closed filters, avoiding any risk of fire or explosion inside themselves. By replacing oxygen with nitrogen or other inert gas, by measuring the amount of residual oxygen, according to the product, there is the certainty of operating in complete safety. Every matter can be addressed, so if there is a need, will operate as part of the ATEX regulations. The main application does not need expensive valves or devices, because it's only 'pneumatically' performing.
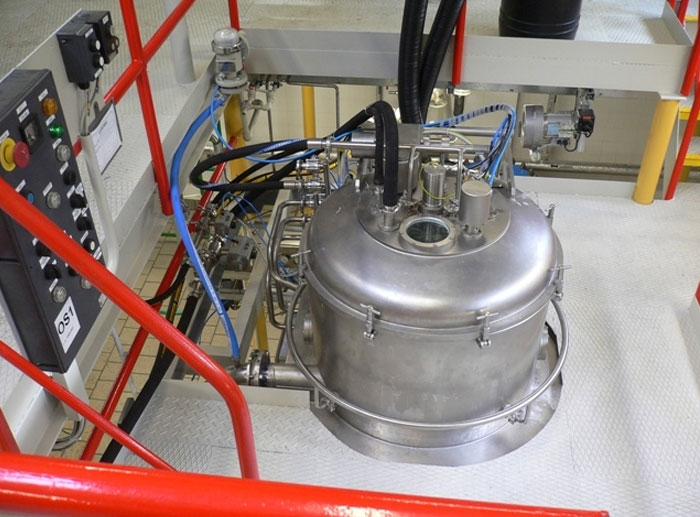